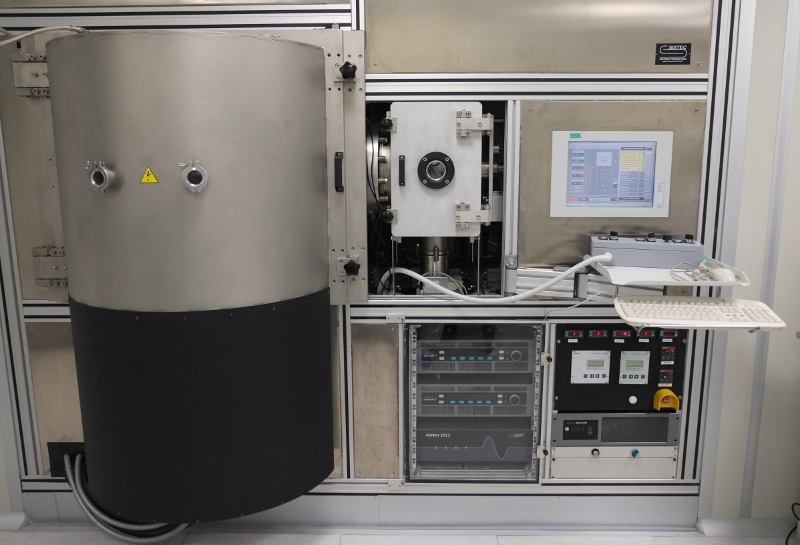
Ion Beam Etching System – Sistec VS80
Details
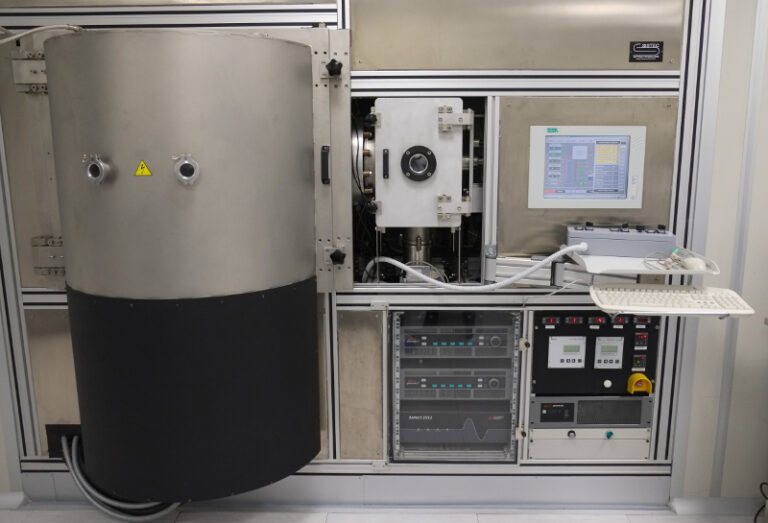
Description:
The VS80 system consists of a chamber for ion beam etching processes, equipped with a KDC 160 Ion Source. A load lock chamber is employed for fast insertion and extraction of samples. The sample holder can fit samples up to 150 mm diameter and is mounted on a motorized stage that can be translated, rotated and tilted in front of the ion source, in order to ensure uniform ablation over the whole sample area.
Working principle
Ion Beam Etching is a physical dry etching technique where Ar+ ions are accelerated towards the sample in a vacuum chamber. Not dissimilarly to what happens with sputtering targets, the sample material is removed by energy transfer between the accelerated Ar atoms and the sample surface. Ar+ ions are generated from inert Ar gas through a discharge current. Here, a filament run by current, which is the cathode, emits electrons by thermoionic effect. These electrons, accelerated towards the anode by the voltage applied between the electrodes (discharge voltage), hit and ionize the Ar atoms giving rise to Ar+ ions and free electrons. These free electrons, which are also accelerated by the potential difference, contribute to maintain the plasma. Some of the Ar+ ions are then accelerated toward the sample by a grid set at a negative potential (accelerator voltage).
Specifications
- Base pressure of the etching chamber ~ 7x 10-8 mbar
- Base pressure of the load lock chamber ~ 10-6 mbar
- Process pressure during Ar-assisted etching ~ 1×10-4– 4×10-4 mbar
- 160mm ion source for etching
- Motorized rotating sample holder for 6” wafers. The sample holder can be tilted (0-90°) for sputtering/etching at oblique incidence.
Ion source for etching:
- Diameter of the beam source 160 mm (6.3‘’)
- Beam voltage 200 -850 V
- Beam current 0.1 – 1.2 A
- Beam neutralizer (filament)
- Performances @ 200V beam voltage, 100 mA beam current
- Etching uniformity on 4”: 95%
- Etching uniformity on 150 mm: 85%
- Etching rate on Titanium: 2.2 nm/min
Sample mounting stage:
- Motorized rotating sample holder hosting 150 mm wafers
- The sample holder can be tilted (0-90°) for etching at oblique incidence.
- The sample holder can be water-cooled.
